Prusa XL Review
The Prusa XL is a high-end Core-XY 3D printer from Prusa Research, the technical specifications of which you can find on their product page. I was recently looking add another printer to my home lab, alongside my trusty Voron 2.4R2, and the Prusa XL was one of several printers I considered - it is also ultimately the one I chose to purchase based on its unique set of trade-offs.
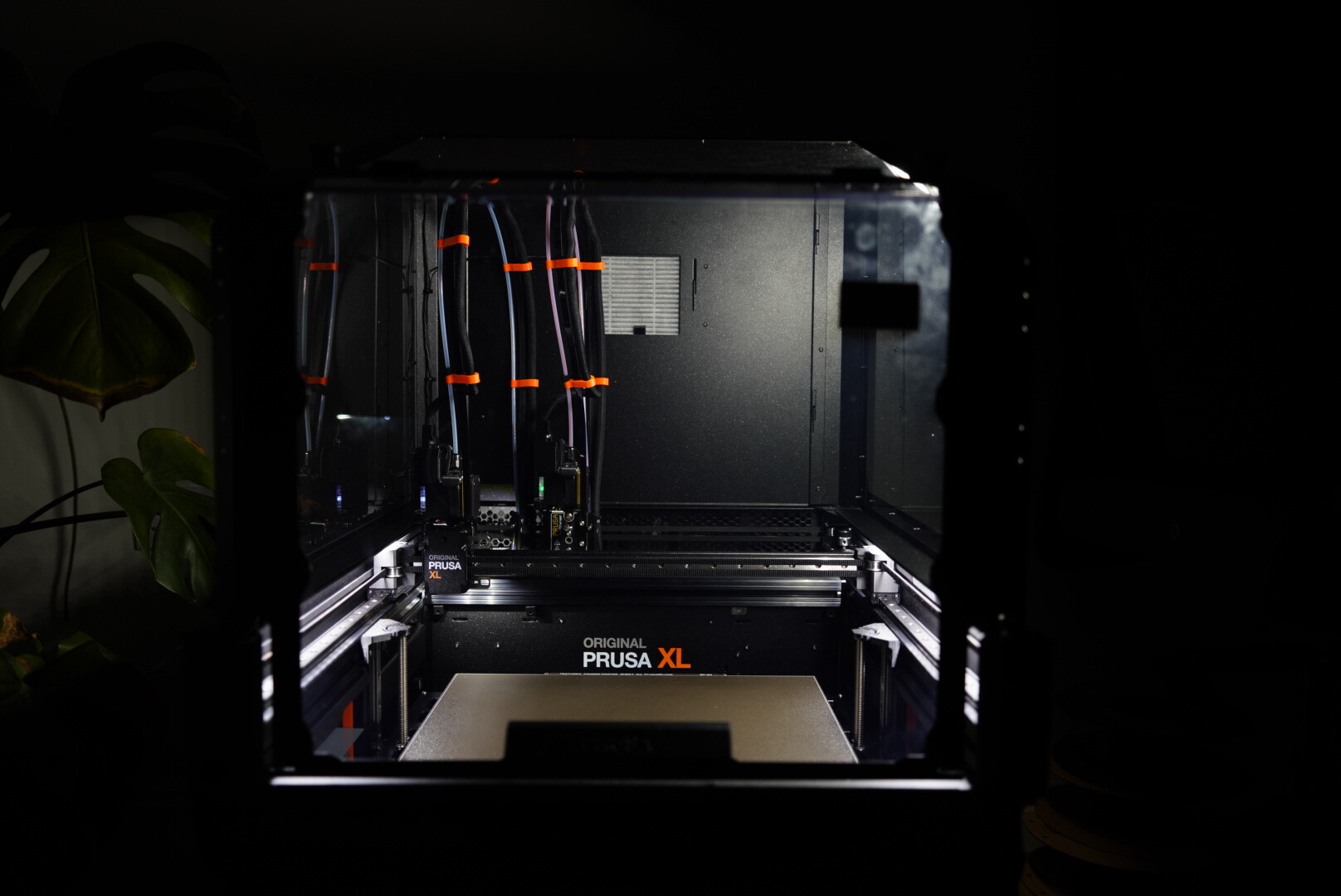
The biggest challenge I faced making this decision was the lack of any deep technical reviews of the Prusa XL, so I'm going to try and close that gap here by sharing my thoughts and experiences through the lens of someone who has spent the last couple of years diving into the guts of what makes for a reliable 3D printer.
My Background
I mentioned that I've got a Voron 2.4R2, which I've been using for the last couple of years. As with most Voron printers, there are many like it but this one is mine. Over the last few years it has evolved from a relatively stock Formbot kit into a machine where very little of the original printer remains. I've run everything from CANBUS, to Tap, to Cartographer, to Xol, DragonBurner, Cartographer Touch (and back again) and moved from a DragonHF hotend to a Slice Mosquito Magnum, I've swapped out motors and drivers, switched to Sensorless, and designed a wide range of improvements to address pain points.
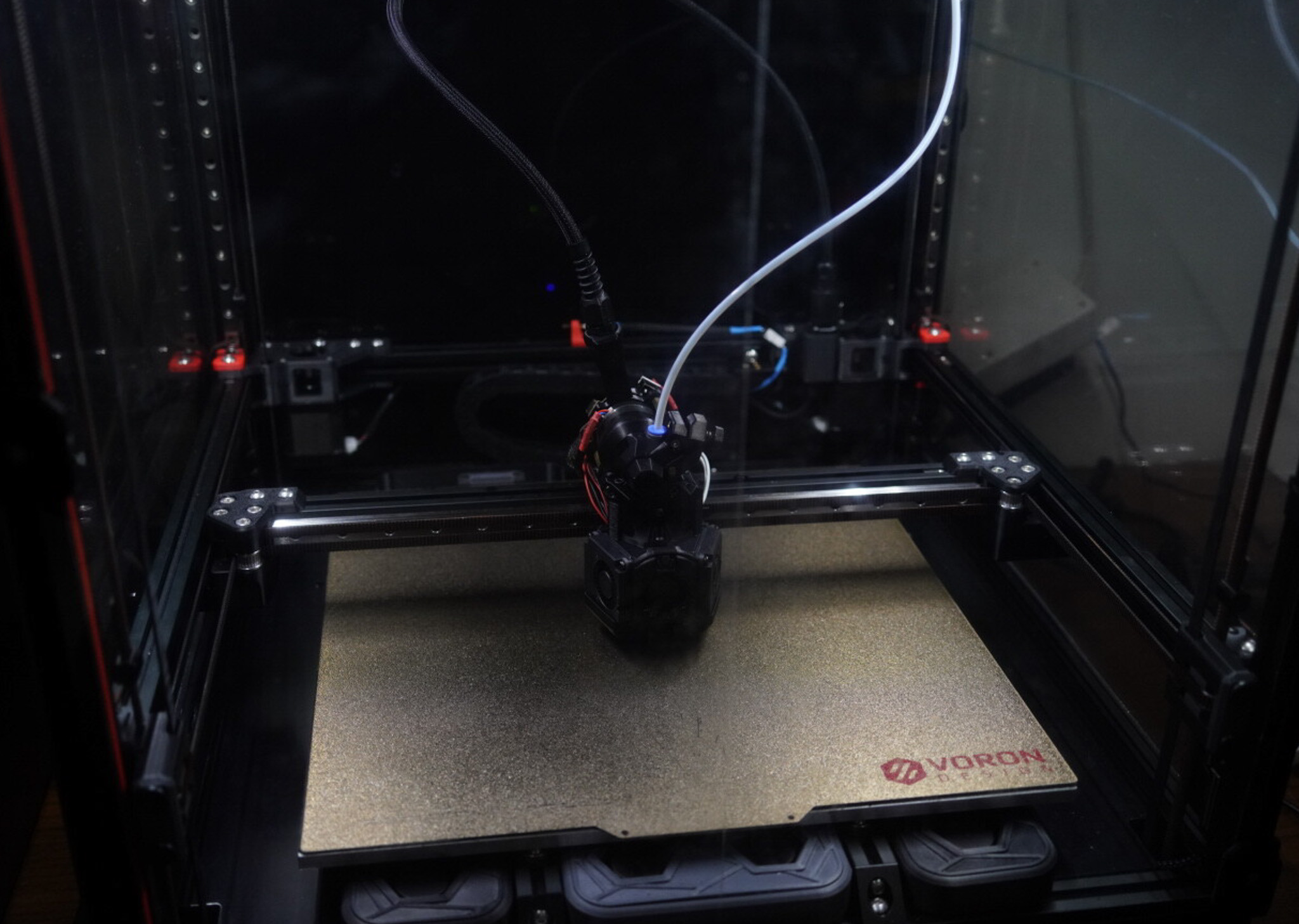
It's fair to say that I've spent well over a thousand hours tinkering and tuning my printer, and that has resulted in a machine which, for the most part, I can trust to just print whatever I need, whenever I need it, quickly and at a quality level I'm happy with. Much of that has been tuning Klipper and my various macros to ensure that the printer is as reliable as possible.
The result is that when I look at a printer, I'm looking at it through the lens of someone who has spent years changing a printer to suit their exact needs: I see it for the issues I know I'll face as I live with it...which brings me to the Prusa XL.
First Impressions
The Prusa XL is unmistakably engineered by people who use 3D printers in anger. Every aspect of it has clearly been thought out to ensure that it will just work, and work consistently, for a long time. It's also clear that, unlike some of the more mainstream consumer printers which have made their way into the market, the Prusa XL is designed to facilitate easy and open maintenance: it reminds me of an old tractor in that respect. There's no sign that you'll need to purchase a replacement gantry assembly if things fail - instead almost everything is either metal, 3D printable, or relatively easy to source (modulo the electronics).
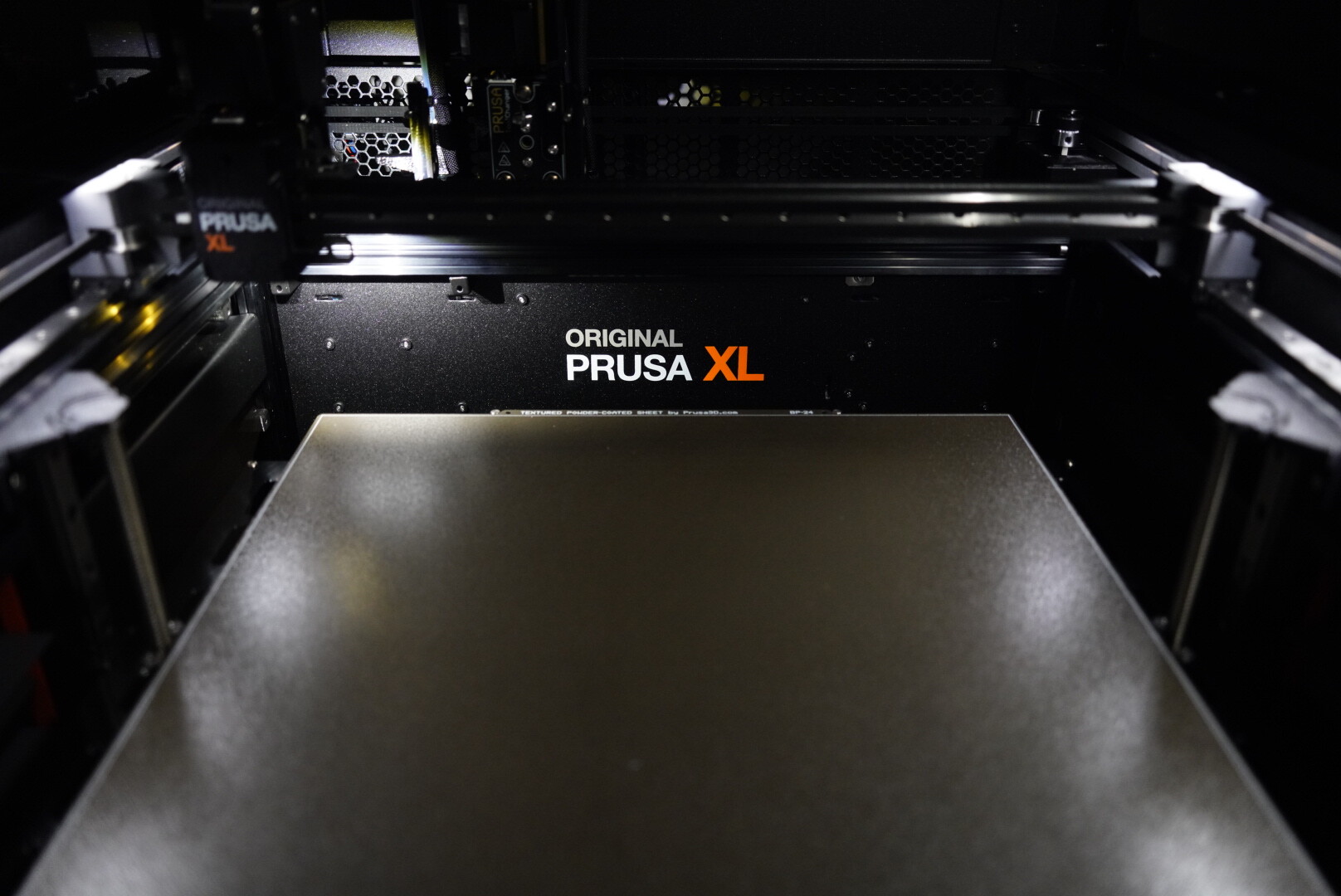
In some respects, it's a bit like a cross-over between the best parts of a Voron (it's yours, you're not just leasing it) and the best parts of an iPhone (it just works, out of the box, with no fuss). The former is why I dismissed BambuLab and Creality's printers, and the latter is why I dismissed options like the Siboor Trident or the RatRig V-Core 4.
Prusa's software ecosystem follows a similar pattern: PrusaSlicer forms the backbone upon which most of our slicers are derived (BambuSlicer/OrcaSlicer) and Prusa Research has consistently contributed open source improvements which have elevated the quality of 3D printing for everyone - however when comparing PrusaLink (the software running on the printer) and PrusaConnect (their cloud management service) against something like Klipper and Mainsail; I can't help but feel like the experience is a long way from the cutting edge (especially when it comes to things like remote camera monitoring, or the integration of additional I/O devices). If Klipper is a Linux server, then PrusaLink is an iPhone - it works well but it's intrinsically limited in terms of what you can do. For most people that's not a bad thing.
The Official Enclosure
Another impression also resonates: this is a printer designed for PLA and PETG. Out of the (substantial) box, it has no enclosure. When assembled, you'll also quickly find that there is extensive ventilation (including room for what could be 5x80mm fans on the back of the printer).
Should you opt to buy the (very expensive) Official XL Enclosure, you'll find that although beautifully engineered and visually striking for all the same reasons that the XL itself is, does little to address the ventilation issue, leaving enough gaps that it likely approximates me leaving one of my Voron's doors open.
Again, for many this won't be an issue - the enclosure will do a great job of preventing drafts and for filaments like ASA or PC-CF, you're likely to be fine. However, for someone like me who has made made a point of ensuring that I can print ABS with minimal VOC emissions, it's a sizeable gap in capabilities.
Another let-down is the lack of software temperature control for the enclosure. The XL's logic board includes ports for additional thermal sensors and the Official Enclosure seems like the perfect place to leverage that capability for filaments which benefit from a certain ambient temperature (on my Voron a chamber thermistor allows me to automate pre-heating and ensure that ABS prints only start when the chamber reaches 45°C). Instead, you're provided with a simple humidity and temperature sensor which provides visual indication of the current conditions but no ability for the printer itself to measure or report on them.
There are of course other enclosures for the Prusa XL, some of which attempt to mitigate these issues - though in my case I opted to go with the Official XL Enclosure because I frankly think it looks better than the alternatives, and I appreciate the tight integration with the printer's firmware. If the XL was based on Klipper and I had the freedom to build my own integrations, I'm sure the story would be very different.
The Nextruder(s)
Depending on your configuration, you'll find yourself with one or more Nextruders (a beautifully integrated toolhead for the XL which includes a custom planetary extruder, a filament sensor, LED nozzle and status lights, and a load cell for contact bed levelling - all in a single, well integrated, package). My immediate impression upon installing these was how well engineered they are. I've run CANBUS on my Voron 2.4 for a while now, and even with a CNLINKO connector and multiple pre-prepared toolheads, the process of adding or removing a toolhead takes at least 15 minutes and requires a lot of careful validation to ensure that everything is working correctly. With the Nextruder, the physical installation takes a handful of intuitive steps, calibration is easy and robust, and I can see how replacing a toolhead in anger would be a quick and painless process. Again, it's clear that this is a printer designed by people who use 3D printers in anger.
Another less obvious, but equally appreciated, aspect of the Nextruder is that the fans are extremely silent and all have tachometers to report RPM. It's a small thing, but fan failures do happen and while a part cooling fan failure is likely to only impact your print, a hotend fan failure can quickly turn into a disaster. Having the printer monitor the RPM of every fan means it can detect fan failures and stalls proactively, and prevent the situation from getting any worse.
This level of care extends to the automated crash detection, which leverages the force sensor and motor-driver StallGuard to automatically detect nozzle and toolhead crashes, something which I have wished for in Klipper for years. It's these little things which make me far more comfortable leaving the printer running without supervision - letting me focus on other things while the printer does its job.
The Firmware Experience
While we're on the topic of things the printer does to keep itself safe, I think it's worth talking about the firmware and design decisions taken by the Prusa team. I've spent years tweaking and tuning my Voron configurations (with over 400 commits to my configuration management repository), and watching the Prusa XL do its thing highlights some brilliant ideas which place an emphasis on safety and reliability over speed and benchmarking.
The first thing you'll notice is the way in which the gantry performs its homing operation. The Prusa XL uses Sensorless Homing which relies on the motor driver's StallGuard functionality to detect when the gantry has reached the end of its travel. This is something many Voron users use, but the Prusa XL takes the process a step further to alleviate a range of failure modes which are all too familiar to Voron users:
- If the print head doesn't move a significant distance during the initial homing operation, the printer will attempt to home on the opposite side of the axis, ensuring that false-positives caused by stiction don't cause the printer to home incorrectly.
- Once the printer has established a baseline zero, it will then perform a series of rapid validation movements testing the X and Y zero stops to ensure that they are correctly zeroed. On a Voron this isn't hugely necessary from a precision perspective - so long as you're broadly in the right area nobody cares if you are 0.1mm off - but with a tool-changer like the XL, this adds a level of accuracy and reliability.
This kind of robust, well thought out, and well integrated experience extends to every aspect of using the printer. Changing filament is a breeze, common maintenance and print tuning options are easily at hand and work well, the initial calibration process is intuitive and works perfectly.
Ultimately, the best thing I can say about the firmware is that it's good enough that I don't think about it (and in many ways it works better than KlipperScreen, which is saying something). Perhaps the most amusing shift in expectations I've faced centers on power management: as someone who has traditionally used a Raspberry Pi to manage my printer, and who has had to be careful about how they restart or power cycle it; I spent a good 5 minutes hunting through menus trying to find how to restart the XL before I realized that the big, red, Reset button takes care of all of that for you. Similarly, the power switch is a perfectly valid way to turn it off. Again, simple, effective, and reliable.
Printing with the Prusa XL
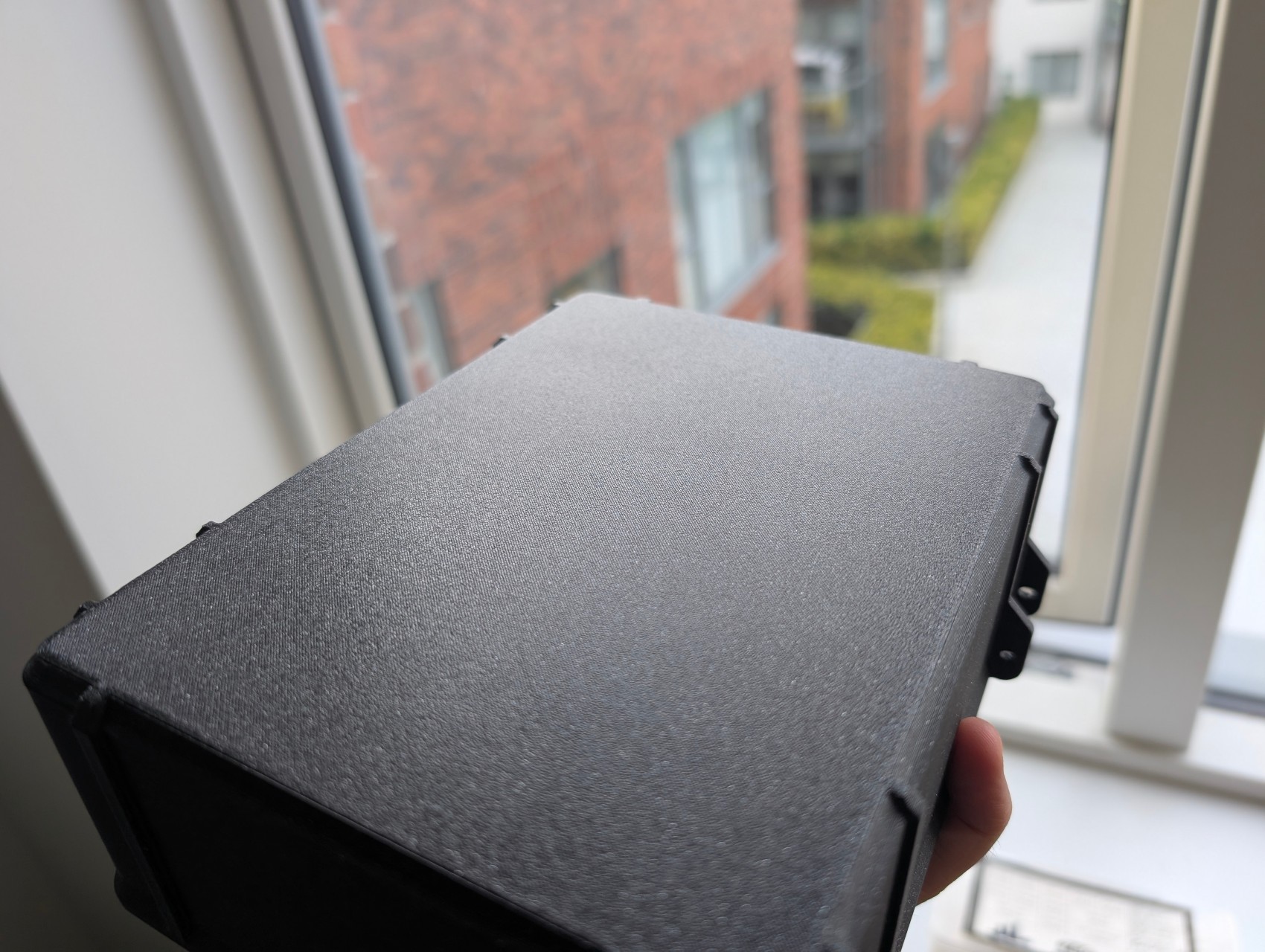
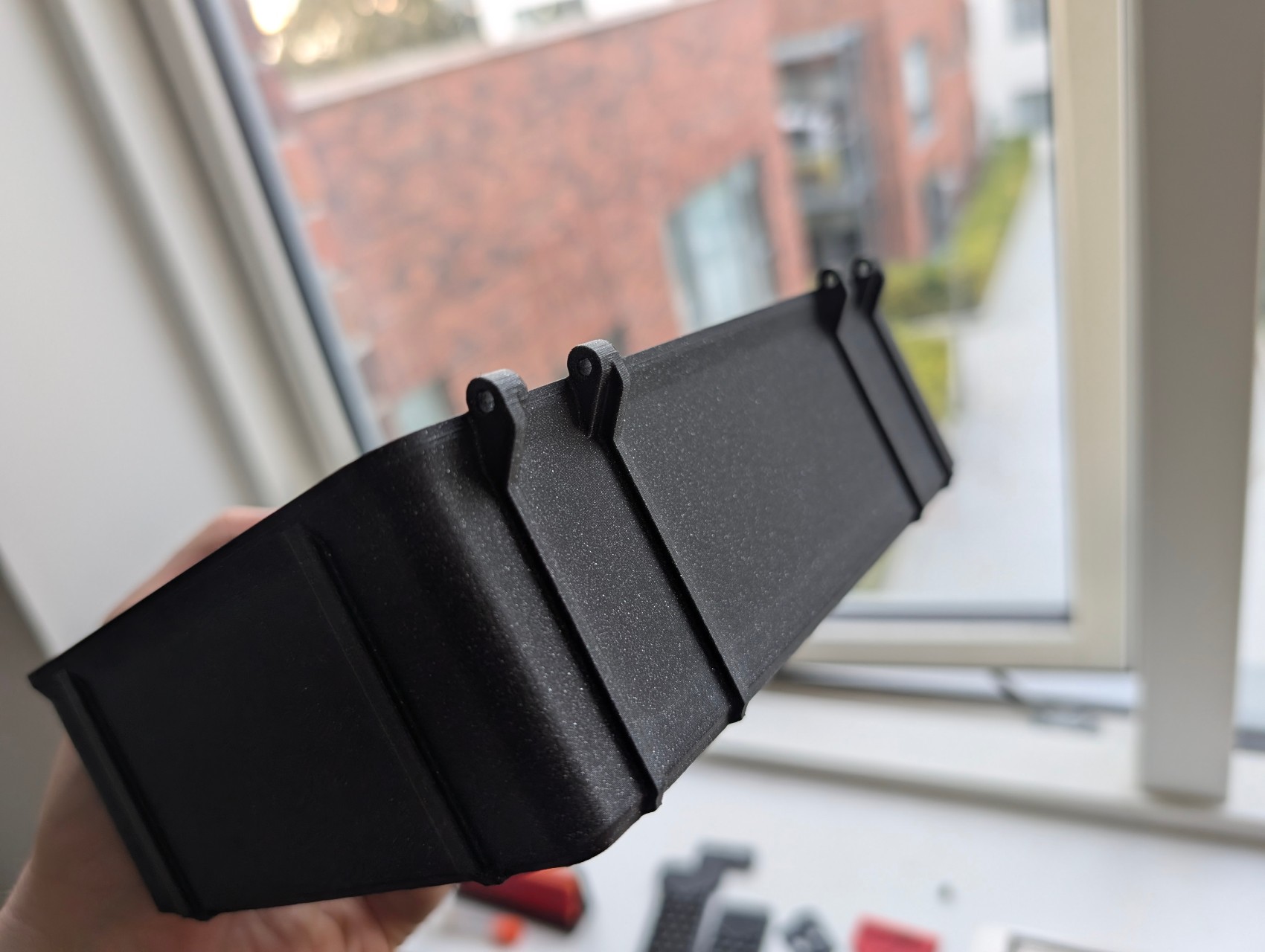
Arguably the most impressive aspect of my time with the Prusa XL so far has been the quality of the prints it produces, with no tuning, input, or other work required. I've tossed everything from Prusa's own Prusament PLA to bargain basement PLA and PETG at it with no fine tuning or calibration, and it has produced flawless prints every time. No stringing, no artifacts, perfect first and top layers, just perfect prints.
This contrasts with my Voron, which required careful tuning before I got anything approaching this level of quality, and which can be fussy enough that I generally just stick to known good profiles and filaments.
That said, the printing experience is not perfect. The Prusa XL is loud. Not just loud relative to a quiet printer (the Voron 2.4R2 when fully enclosed and running StealthBurner is fairly quiet when running in another room), but loud enough that it is disturbing on the other side of the house. For all the work done to ensure the fans are quiet, the XY gantry movements, even on "Stealth" mode, are loud enough to raise eyebrows.
I had hoped the enclosure would help cut down on this noise, however that has not been the case in its stock configuration. Part of this likely stems from the significant ventilation provided in the base configuration, and part of it likely stems from the XY motors being exposed rather than enclosed as is the case for the Voron 2.4R2.
If you're looking for a printer which is quiet enough to run in a shared space, or to run overnight in a room adjacent to your bedroom, the Prusa XL might not be the right choice. It's also worth noting that this is most noticeable on travel moves, so tuning maximum acceleration and speed settings for your profile might get the printer to a more suitable level at the cost of print times.
Print Speeds
It's worth noting that the Prusa XL is not intrinsically designed to be a fast printer. The Nextruders, for all of their wonderful engineering, are heavy toolheads whose center of mass resides a long way from the X-rail. Said X-rail is an MGN-12H attached to a relatively small support structure and moved with 6mm Gates GT2 belts - all very familiar for a Voron user. Those 6mm belts are longer than you'd find on your typical 350x350mm build volume to accommodate the tool-changer, and all of that leads to a printer whose maximum acceleration tops out at for travel moves and a pedestrian for infill moves in the default "Speed" profiles.
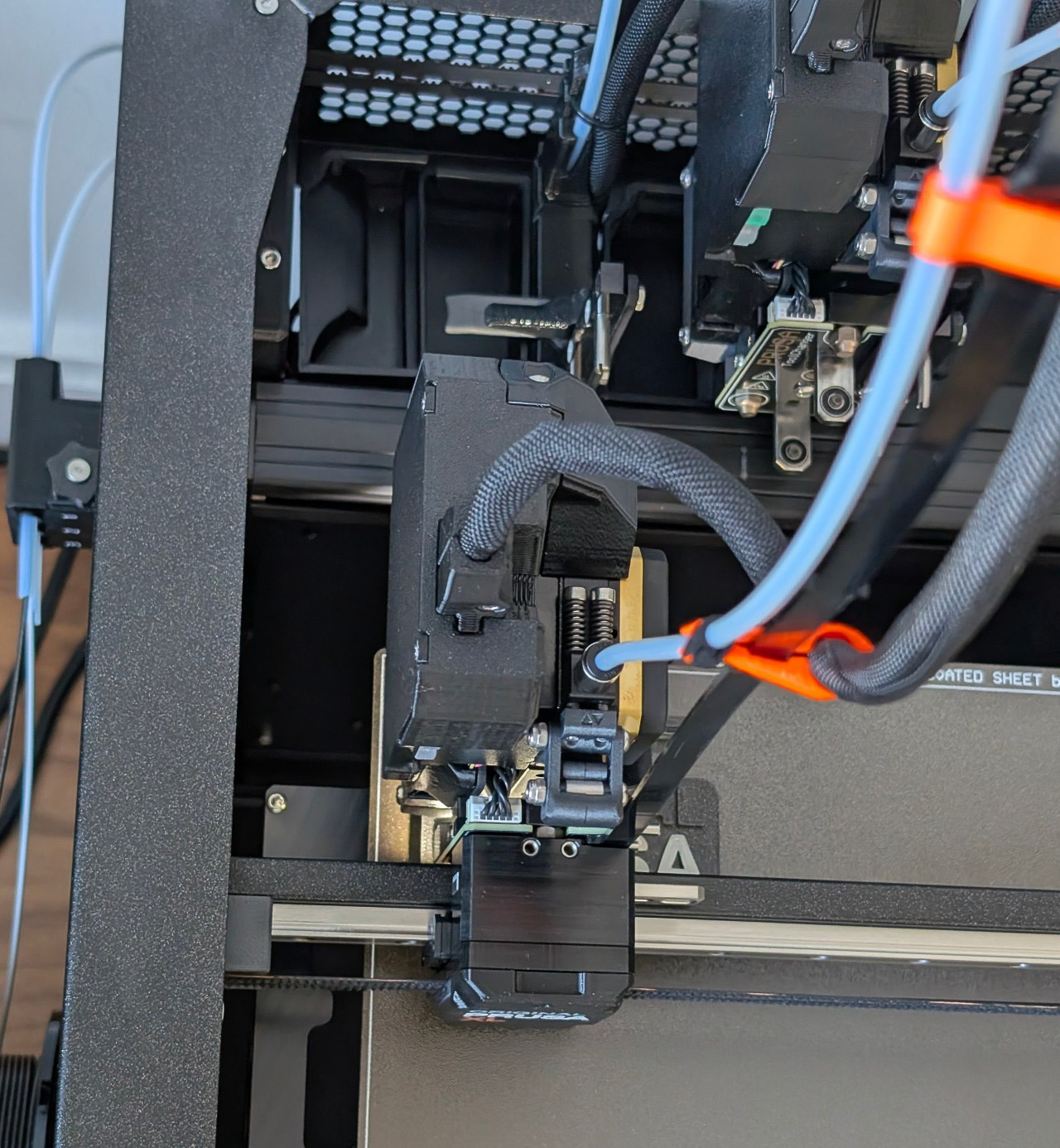
Contrast this with the work the Voron community has done to push the limits of the 2.4 and Trident platforms, with accelerations in the range being easily achievable for travel moves, and AWD configurations being able to push for infill moves. The net result is that in a basic speed race, the Prusa XL isn't going to win any prizes - and this is further exacerbated by its careful and ponderous pre-print setup process (which clocks in at well over 5 minutes before laying down the first layer - in contrast to the mere 1m20s for my Voron to do the same thing).
That said, the Prusa XL isn't designed to compete on raw speed. It's designed to be run in a 5-toolhead configuration, producing complex engineering parts with a combination of different materials, colours, and low cost supports. The moment you start to play that game, the Prusa XL really dusts off its gloves and gets to work. There are some great comparative reviews of print times and defect rate for multi-material prints - comparing the BambuLab AMS to the Prusa XL and demonstrating that the XL is at least twice as fast, and with a failure rate orders of magnitude lower than the AMS.
By opting to use a tool-changer, the Prusa XL avoids an entire class of potential failure modes which plague other multi-material configurations, and doesn't require slow or wasteful workarounds to mitigate them. Of course, it does introduce a new class of failure mode: a failure to correctly align each of the tool-heads with one another can result in imperfections where the materials meet. Fortunately, the Prusa XL uses a reference pin and a comprehensive automated calibration routine to address this for you. In practice, the results I got after completing the calibration routine were perfect, with no visible imperfections or differences in output quality between the different materials.
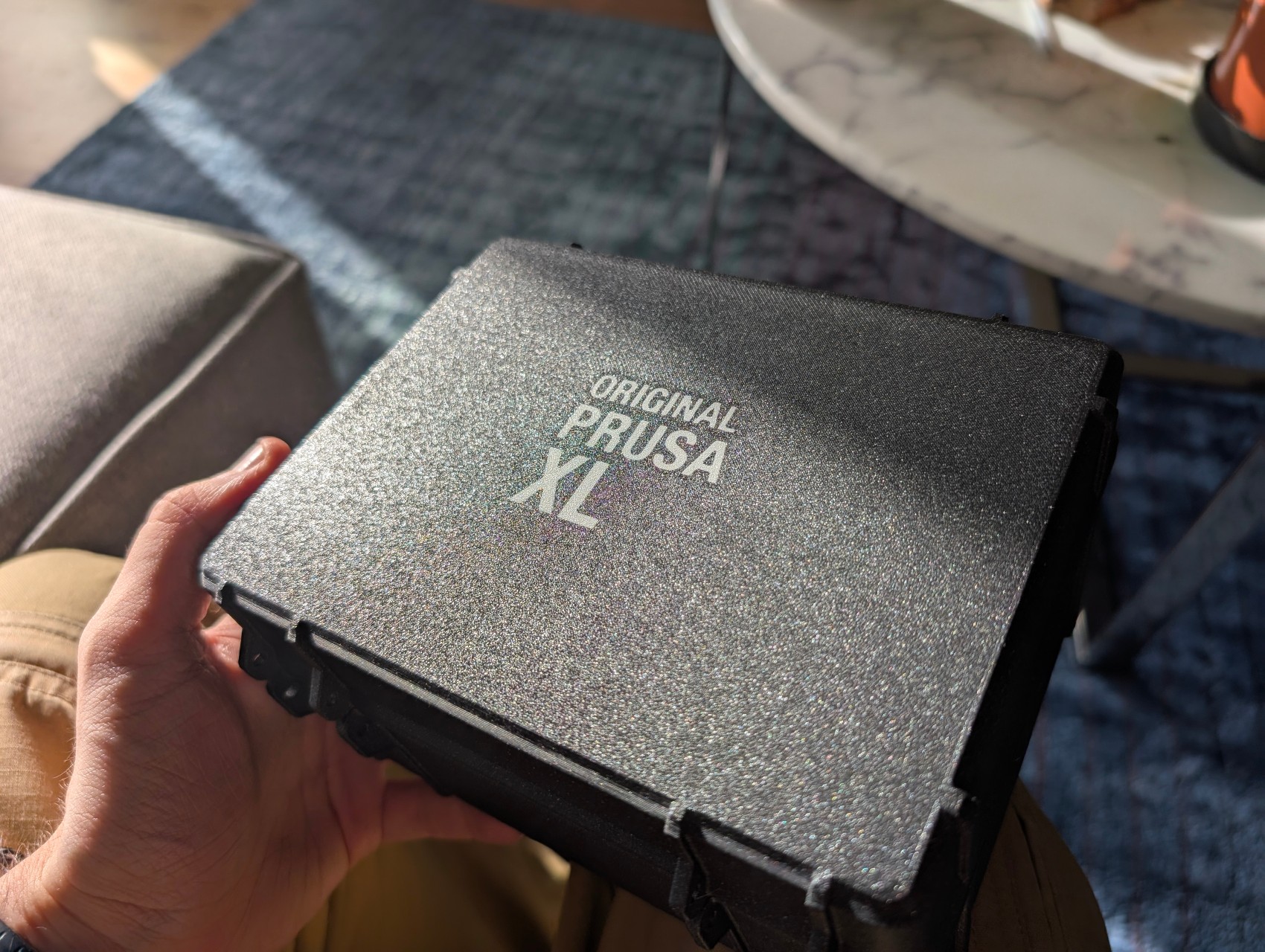
I can attest to the fact that on the XL, printing in multiple materials is quick and easy enough that I don't consider it as a factor in my print planning, instead focusing on what I'd like to design rather than on whether it's worth the extra time and effort to print it in multiple materials. In practice, the amount of waste material is also significantly lower than filament changer setups like ERCF/MMU/AMS, with the XL only performing a quick priming purge after each change (and even this can be skipped if you're using compatible filaments and are willing to purge into the infill), but given the cost of the printer it's unlikely you're going to be saving money any time soon by doing so.
Practical Accuracy
The model I generally use for accuracy testing is the Vector3D Calilantern which provides both an accurate assessment of linear errors (scaling) but also skew (rotational transforms) generated by physical imperfections in the printer's assembly. The Calilantern reports a score in the range with representing absolute perfection and representing of skew and scaling error on all axes. In practice, I've found that scores are more than good enough for most practical engineering purposes.
In my case, the Prusa XL spits out a score of without any tuning or calibration, with an average skew of and a uniform scaling error of which can easily be corrected in the slicer for this filament. I would consider this an exceptional result. To put that into perspective, it's good enough to hit 0.2mm tolerances on a 100mm part - as I said, exceptional.
Is the Prusa XL worth the cost?
Subjectively, yes. The Prusa XL is a beautifully engineered printer which serves the purpose I bought it for perfectly: a printer which gets out of the way and lets me focus on what I want to design rather than on how the printer works, while allowing me to add a capability to my home lab which I didn't have before (namely multi-material and multi-colour printing). That said, a 5-toolhead Prusa XL with the Official Enclosure comes in at roughly the same cost as 6 BambuLab P1S printers with the AMS combo, all of which are able to print multi-material and multi-colour prints and include an enclosure with far better sealing and thermal management than the Prusa XL.
As a first printer for a hobbyist, I think the Prusa XL is a poor choice. It's expensive, niche, and for most users it's unlikely to offer a compelling argument over something far cheaper. For a professional who needs a reliable tool capable of mixing materials (especially things like PVA supports), I think you'll be hard pressed to find a better option at the price point. And finally, for the hobbyist who is looking for Adult Lego, I think options like the Siboor Trident AWD or RatRig V-Core 4 offer a more compelling framework to build and tinker, while still offering incredible capabilities, at half the price or less.
The Prusa XL fills a very specific niche, but for the right user, I can't think of a reason you won't be very happy with it sitting in your workshop - I know I am.